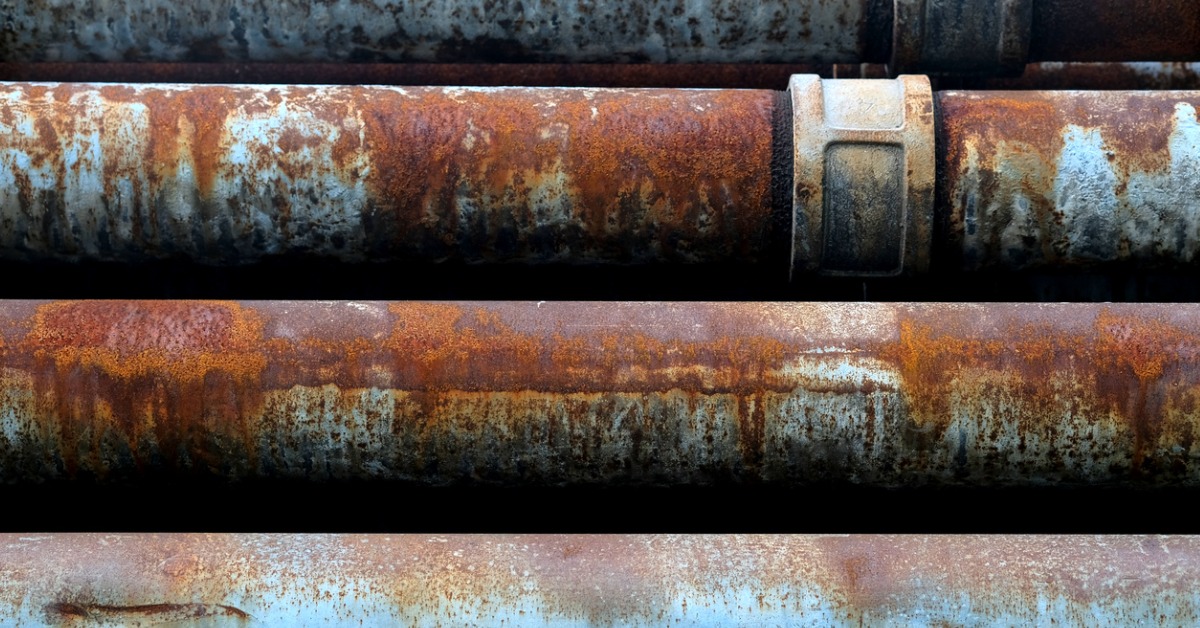
The terms corrosion and rust are often used interchangeably. While they’re both the result of oxidation, the two are actually different. Here, we take a look at rust and corrosion, including the types and what you can do to prevent them from occurring.
What is Rust?
Rust occurs when a metal is exposed to moisture or air. This causes a red or orange coating to appear on the surface of metals - usually iron and its alloys. Without the presence of iron, a metal can’t rust. Rust is defined as iron oxide, a compound of iron and oxygen.
There are three types of rust - red, black and white.
Red Rust
Red rust is produced from a mixture of oxygen, iron or steel, water and time. The iron or steel usually deteriorates fast when red rust is present compared to other types of rust.
Black Rust
Black oxide or black rust is the harder layer beneath red dust. Black rust usually occurs in a low oxygen environment. It binds to the base material and provides partial protection from further oxidation.
White Rust
This form of powdery white rust usually occurs on zinc plating after being exposed to the atmosphere.
What is Corrosion?
Corrosion occurs when materials deteriorate due to chemical or other reactions. It can affect a range of different materials such as wood, copper, and bronze. Ceramics and polymers can also be impacted by corrosion, but that’s known as degradation.
From uniform attack to selective leaching, there are multiple forms of corrosion that you should be aware of.
Uniform Attack
Uniform attack is the most common form of corrosion. It occurs when a chemical or electrochemical reaction proceeds uniformly over an exposed surface. Uniform attack causes a metal to become thinner and eventually fail. It causes the greatest destruction of metal per tonne.
Galvanic Corrosion
When two different metals are immersed in a corrosive or conductive solution, and the metals are in contact or electrically connected, an electron flow occurs between them. The less resistant metal becomes anodic, with the more resistant metal becoming cathodic. The cathodic metal corrodes very little or not at all.
Crevice Corrosion
Intense localised corrosion occurs within crevices where stagnant solution occurs, such as under bolts and rivet heads.
Pitting
Usually recognised as relatively small holes, pitting can appear on piping as a rough surface. This intense form of corrosion can cause failures to occur extremely suddenly.
Intergranular Corrosion
Intergranular corrosion occurs in the grain boundaries of stainless steel, which is mainly caused by chromium depletion.
Erosion Corrosion
The accelerated rate of deterioration or attack on a metal is caused by relative movement between a corrosive fluid and the metal surface. Grooves, gullies and rounded holes appear and failures can occur in a fairly short time frame.
Stress Corrosion Cracking
Cracking occurs due to the simultaneous presence of tensile stress and a corrosive medium. The metal or alloy is unattached over most of its surface, but fine cracks occur which can cause stress to the medium.
Selective Leaching
The removal of one element from a solid alloy causes the corrosion process, such as the selective removal of zinc in brass alloys.
Where Do Rust and Corrosion Occur?
Any iron and alloy is at risk of rust. Metal objects that come into contact with water are most at risk, such as water tanks, water pipes and several other materials that can corrode. However, the industries with the biggest repair bills are the gas and oil industry, as well as maritime and manufacturing industries.
Preventing Rust and Corrosion
The effects of corrosion create a damage bill of between 3.5 and 5.2 percent of global gross domestic product. For Australia, that equals $78 billion spent every year remediating assets affected by corrosion. A significant contributor to these costs is remediating water pipes.
There are several ways to prevent rust. Storing metals in low-moisture areas or inside temperature and humidity-controlled environments will significantly slow down the effects of rust. For most metals, there is no escaping damaging effects of the environment. Coatings such as paint, oil, galvanising, powder coating and blueing can protect metal surfaces.
However, for some metals, the area most at risk of rust and corrosion can’t be coated. Water pipes and fittings such as shower heads and taps require treatment from the inside with a dispersing agent. Mining companies, as well as commercial and residential building operators and hotels are using Acquasolve to tackle corrosion and scale build-up. The scale inhibitor in Acquasolve coats the insides of pipes to stop scale crystals from forming.
For more information about Acquasolve, call us on 1300 29 32 32 or contact us online.